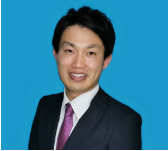
おはようございます!
カイゼン研究会の宇賀です。
プロフィールはこちら↓↓↓
http://japan.a-solsh.com/staff_details23.html
中国の工場では日常茶飯事となっている
計画変更について話していきます。
「お客様の急な追加やオーダー変更が、、」
「納入された部品に不良が、、」
などなど
様々な理由で計画変更が余儀なくされます。
むしろ、計画通りの方が珍しいくらい日常化しているのでは
ないでしょうか?
そして、それを上手く調整し乗り切っていく管理者が
現場で活躍している状況が中国では多いです。
今回は、当たり前の仕事になってしまっている
計画変更を見直してみようという話です。
(1)ここで言う計画変更とは何か?
(2)計画変更を引き起こす要因
(3)異常を隠さないためにすること
この順番で説明していきます。
(1)ここで言う計画変更とは何か?
会社によって様々な生産計画が使われているのですが
大きく分けると以下の3種類になります。
1.内示及び受注ベースの生産計画(1カ月〜3カ月分)
2.受注及び出荷ベースの生産計画(1日〜1カ月分)
3.製造による仕掛け順ベースの生産計画(1日分)
(当日計画)
1つ目は
お客様からの内示(予測)ベースや
早めに確定している受注を使った長い期間での
生産計画です。
おおよその生産量を把握するのが目的で
材料の購買や人員の調整に使用されます。
2つ目は
実際の受注ベースと出荷日、お客様への納期を踏まえて
生産を実行するための計画になります。
基本的に生産管理が作成し、
多くの工場で「生産計画」と呼ばれているものはこれです。
これをもとにして、
納期遅れの把握や生産実績との比較を行うなど
生産が良かったか悪かったかを判断するものとなります。
以降は
生産計画と呼びます。
3つ目が
生産計画をもとに
各製造が
作る順番を決めて
実際に作業員に指示だしするための
仕掛けベースの生産計画です。
(当日計画)
プレス、加工、などではロット生産を考慮し、生産順序を決めます。
組付では主に生産順序を決めたものになります。
以降は
当日計画と呼びます。
この当日計画はほとんどの工場において
製造しか把握していないのが現状で、
生産管理や上層部は2つ目を生産計画としてみています。
そして
今回話したいのは
3つ目の
当日計画を変更した場合です。
当日での急な変更になり、手待ち、ムダな段替え及び材料運搬
人員配置変更など様々なロスを引き起こします。
その上これらは管理者も知らない間に起こります。
(2)変更を引き起こす要因
冒頭で挙げたように
お客様の急なオーダー変更、納期変更や
使おうと思った時に、部品や材料に問題があり
使えない場合というのが、よくある突発の当日計画変更です。
これらは
外部要因による当日計画変更で
社内ではコントロールしづらい要因になります。
管理者に報告で上がってくるのは
この外部要因だから仕方ないというものがほとんどです。
しかし
本当にそうなのでしょうか?というのが着眼点です。
実はよく観察してみると
内部要因の当日計画変更は
かなりあり、ロスを発生させています。
なぜ見えにくいかというと
先ほど挙げた2つ目の生産計画の
生産台数は達成されていることが多いからです。
内部要因で異常が出ているにもかかわらず
生産順序に変更を加え、調整し
生産台数は確保するということを製造は
日常的に行っています。
本来は前日に決まっている
当日生産計画の順序で生産するはずが
順番を変えることで異常が見えない状態になっています。
組付ラインで起こる内部要因の例を挙げます。
当日の朝、組付ラインでは
前日に作成した
当日計画に沿って生産しようとします。
しかし、この当日計画は組付ラインが独自に決めた
仕掛け順序です。
他の前工程や倉庫・物流も同様に
組付の生産に対して
数量が間に合うような
当日計画を各々が作って動いておりますが
組付が使う順番までは知りません。
そして
いざ組付が生産しようとすると
・前工程にまだモノがない。(午後には完成するはず)
・倉庫で外注部品の運搬準備ができていない
・前工程から運ばれる順番が間違っている
・後工程引き取りの場合は、
スペースの問題で欲しい品番が運び出せないくらい奥にある。
などなどの問題が発生します。
その状況に直面して
組付ラインでは当日計画(生産順序)を変更します。
そして治具の段替えや
すでに運搬された部品の入れ替えなど
走り回りながら調整し、何とか生産台数を間に合わせます。
この例の中には3つの問題が潜んでいます。
1つは
工程間で当日計画が同期されていないということ。
組付の当日計画を基準として、
前工程がその順序に合わせて出荷できるか。
前日時点で全工程摺合せしたうえで、
当日計画を作れていれば、
内部要因での計画変更はかなり防げます。
外部要因が起きた場合のみ、
当日計画に変更が生じるというのを当たり前にしないといけません。
2つ目は
当日計画変更でロスを出しながらも
残業が増加しているなどの異常は見えず
生産台数を達成しているということ。
つまり、実はかなり余力を持っているということです。
そのロスが吸収できるくらいの標準時間が設定されているため
異常が起こっても、顕在化しないというのが大きな問題です。
(カイゼンする場所を発見できない)
3つ目は
当日計画の変更が異常だと認識されていないこと。
残業込みで12時間稼働だとした場合
12時間内で生産完了できれば良い、異常なしという
仕事の方法が行われているということです。
(3)異常を隠さないためにすること
・当日計画を可視化し、固定すること。
現状は製造しか知らない情報なのですが
どれだけ遅くても、当日の朝には決まっている計画です。
その確定した当日計画を、紙でもシステムでも良いので
表示させ、その順番が今日の基準だと認識するようにします。
・当日計画の変更は異常ととらえること
上で決めた当日計画通りに作れない場合
例えば、3品番A、B、Cがあり
A→B→Cが確定した生産順序だったが
B→A→Cの順番で生産してしまった場合。
は日報に原因を記入する。
・上記のために数量ではなく時間の管理を導入すること
当日計画を可視化する際に
開始終了予定を品番ごとに設定された標準時間を使って
計算しておく。実際の開始、終了時間も記録する。
生産管理板のように
時間での予定と実績を記録しておかないと
そもそも当日計画の変更には気づけないのです。
この3点を実施することによって2つの異常が見えてきます。
・当日計画変更を起こしている異常
→数量さえ達成していれば生産順序は製造に任せるからの脱却
・予定時間と実績の差を生んでいる異常
→数量でなく、時間通り作れない理由にカイゼン代がある。
→もしくは、標準時間が実態とかけ離れている。
この2つの異常を、すぐに解決しなくてもよいので
記録して残すことが重要になってきます。
そして
その異常の蓄積の中から、
今年、来年、工場として取り組むべきテーマを
決めることのできる状態を作っていくことが理想です。
長々と書きましたが
最後までお読みいただきありがとうございました。
P.S.
まずは工場内で、様々な呼び方や種類がある
生産計画とその目的を整理するところから
やってみることをお勧めします。
ブログをはじめました!
https://kaizenlab.hatenablog.com/archive
過去のメルマガはこちら!!
↓↓↓
https://a03.hm-f.jp/817/index.php?action=ViewBnSetting&gid=3#
wechat(微信)でも配信中!!(中国語版も)
一般社団法人 生産、物流現場カイゼン研究会 中国支店
カイゼニスト 宇賀 邦人
======= この定期カイゼン通信の目的 =======
この定期カイゼン通信は、生産現場、物流現場で孤軍奮闘されている管理者の方へ、また、中国ならびに東南アジアのオペレーションを管理している方へ少しでもお役に立てればと思い、発行させていただいております。
我々は、生産現場、物流現場の皆様が抱える問題を様々な方法で解決し、
カイゼンする事を第一の仕事としております。
品質のカイゼン、生産性のカイゼンなど、様々な成功事例が当研究会には
数多く蓄積されています。
その事例を皆さんでシェアすることが、最短距離での解決方法ではないかと
思い、ニュースレターを発行しています。
お問合わせや、お聞きになりたいことがありましたら、このメールに直接
返信して頂いて結構です。
当研究会では、しつこい売り込みは一切ないので、安心してお問い合わせ下さい。
ご相談は24時間、365日無料で対応しております。
******************************************************
当研究会の理念は「感謝」です。
当研究会の仕事は、「現場で起こった問題をトヨタ生産方式(TPS)やITを
活用して解決し感謝される事」です。現場で困ったら、まずはご一報を!!
相談無料です。
http://www.a-solsh.com/index.html
******************************************************
ご連絡は中国からは400-604-1765フリーダイヤル、
24時間365日受付中、日本、東南アジアからは
TEL:+86-21-6440-1765 /86-21-6432-5544
受付時間は平日9:00〜18:00までです。
生産、物流現場カイゼンNews Letterはこちら!!
http://www.a-solsh.com/mailmagazine.html
http://www.a-solsh.com/center01.php
一般社団法人 生産、物流現場カイゼン研究会 中国支店
上海市長寧区広順路33号C南座206室
お問い合わせ:
marketing@a-solsh.com
メール配信解除は下記URLをクリックして下さい。
https://a03.hm-f.jp/index.php?action=C1&a=817&f=7&g=3&c=30364&m=361&code=4951c4f5f74753ed84f17d384bc13dc2&fa_code=09c371595ff20f033f057ed2ee6027a0