得意先からの電話が鳴る。
嫌な予感。普段、私に連絡が来ることは稀だ。
現地責任者として赴任してからもう2年たつ。
現地の工場長や部長もいるのだが
日系企業ということもあり、
重大な問題は、お客様や本社から直接連絡が来ることに
なぜか慣れてしまっている。
電話に出ると
悪い予感通り品質不良へのクレーム。
品管を早急に得意先へ向かわせ
製造、物流に巻替え品を出荷するよう指示を出す。
「この不良、まえもありましたよね?」
この言葉が頭で復唱される。
おっしゃる通り、たしか半年ほど前に
同じような不良を出してしまっている。
もらったクレームの内容はだいたい覚えているが
再発防止書まで目を通して確認したはず。
急いで、前回の再発防止書を見に行く。
そう、たしか異物や材料間違いを防ぐために
作業者のチェック項目を追加し
それに加えて、人も増やし目視検査の工程も新設したはず。
チェックが漏れたのか?
いや、標準書も作らせたはず。
作業者も人なのでミスは十分にあり得る。
標準を守らず作業していたのか?
守っていたがミスしたのか?
どちらにしろ、現に再発しているじゃないか。
次の再発防止対策を考えさせないと
――――――――――――――――――――
おはようございます!
カイゼン研究会の宇賀です。
プロフィールはこちら↓↓↓
http://japan.a-solsh.com/staff_details23.html
今回の話はクレームが発端となっておりますが
現場の見える化でもなんでも
異常が発見された後にどうするか?が
今回のテーマです。
異常を再発させないためには
何ができるかということを考えて、対策を打つのが
製造業における本質的な仕事となります。
再発防止という呼び方はあまり好きではないですが
この異常解決、問題解決というのが
異常発見とセットになって初めて効果が出ます。
そして、先ほどの再発防止できなかった例のように
これが一番スキルの必要な分野でもあります。
異常が起こった後に
「再発防止しときなさい」ではおそらくできません。
各社、様々な再発防止書のフォーマットがありますが
共通しているのは
原因分析(5回のなぜなど)に重点が置かれ、
それに対して対策を実施するという流れです。
ここで問題になるのは
この原因分析はフォーマットが自由なため
人によってかなり違う結果になってしまうこと。
対策をすでに思いついたもしくは実施しており、
それに合わせるための原因分析なっている等々。
上司にとっても満足のいく内容がなかなか出てこない
という悩みはどこの会社にもあります。
しかし、
何度も同じ問題が起こらないようにするためのコツや
再発防止書のチェックポイントは
実は因果関係の美しさや深さではなく
(1)スタート地点
(2)網羅性(漏れなくダブりなく)
この2点が重要です。
まず、1点目のスタート地点です。
問題解決のSTEP2、問題の層別にもつながる話ですが
あくまで再発防止のフォーマットに沿って話します。
スタート地点とは原因分析を始める場所ということです。
言い換えると問題を何とおくかということです。
先ほどの例では、
・標準を守らなかった
・確認ミスをしてしまった。
として
なんでそうなったかという思考になっていきます。
その結果
次の再発防止書による対策は
ダブルチェックの追加や
従業員への教育
というものが対策になってくるという流れです。
そんなの当たり前じゃないか、、
原因分析は人のせいにしてはいけないという
ルールもあるし、そうならないように心がけています。
という思いもあると思います。
しかし、実際は
分析を開始するスタート地点が
「異物混入」や「材料誤投入」など
より大きなところから入らないと
先の例のように、また再発してしまうことになります。
なぜ、より大きな問題から始めないといけないかというのが
2点目の網羅性につながります。
基本的に再発防止というのは
すべてのリスク、可能性を一つずつ消していく作業です。
こういう場合
工程やプロセスを洗い出し
発生源を突き止めるという作業があり
そこに対策を打つのが通常の再発防止ですが
ほとんどの問題において発生源(問題点)は1点ではないのです。
材料誤投入の例で言うと
以前の再発防止では、投入する部分を発生源として
それが起こらないように対策を行ったはずです。
しかし、もっと範囲を広げ
その作業のスタートから終わりまでを見ること
これが網羅性です。
・生産指示、材料指示
・指示に合った材料の出庫
・材料の現場までの運搬
・材料の投入
・完成品の検査
プロセスを一つ一つ見ていくと
モノと情報が動いていく中で
すべての工程で間違うリスクがあると言えます。
・顧客のオーダーと指示が違う可能性はないのか?
・指示通りの材料以外を出庫するリスクはあるのか?
・運搬の際に間違えることはあり得る環境なのか?
・投入の際に必要な材料以外も投入できてしまうのか?
・検査は何と何を比べ、材料が違っていると判断するのか?
こうやって見ていくと
そんなことは起こるはずないと
作業者は言うかもしれませんが
絶対とは言い切れない箇所はすべてリスクなのです。
問題解決手法のSTEP2問題の層別では
この中でリスクや影響度を考慮して優先度を決めていきますが
あくまで、顧客クレームによる再発防止の最終目標は
そのリスクをすべて消すということです。
各プロセスでどんなリスクがあるか
細かく現場でのオペレーションを見たり
使われている情報(帳票やエクセル)
でミスが起こり得ないかを確認していきます。
各プロセスにすべてチェックを追加するというわけでなく
こう見ていくと、工程をまたぐ重複作業やチェックが
存在することが見えてきます。
それをどうなくし、楽にして
尚且つリスクを減らすかというのが
対策になってきます。
現場のミスのように扱われていたが
実は生産管理の出す生産指示の帳票の内容を変え、
出庫する権利(引換券)のように利用すれば
あとの工程でのチェックや、違う帳票の運用も不要だよね
というような対策につながっていきます。
なので、この網羅性
問題が起こる可能性がある個所を100%洗い出しきる。
そこから、ここは大丈夫だよねと絞り込んでいくというのが
再発防止、問題解決でのコツとなります。
再発防止をチェックする方はこのポイントを押さえて
部下の再発防止にアドバイスを出していくことで
先の例のような状況を減らしていけるかもしれません。
長々と書きましたが
最後までお読みいただきありがとうございました。
P.S.
中国各地の工場で
問題解決手法を使い、
工場の実際の問題を解決していく
実践型教育を行っております。
やっていく中で気づいたのが
今日話した
・スタート地点
・網羅性
これに気づけることで
対策の精度が格段に上がってくるということ。
原因分析のすばらしさ、深さももちろん重要ですが
中国の管理者がまずコツをつかみやすいのは
この2点です。
ブログをはじめました!
https://kaizenlab.hatenablog.com/archive
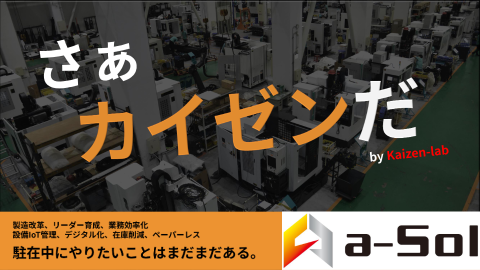
過去のメルマガはこちら!!
↓↓↓
https://a03.hm-f.jp/817/index.php?action=ViewBnSetting&gid=3#
wechat(微信)でも配信中!!(中国語版も)
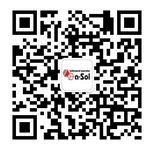
一般社団法人 生産、物流現場カイゼン研究会 中国支店
カイゼニスト 宇賀 邦人
==== この定期カイゼン通信の目的 ========
この定期カイゼン通信は、生産現場、物流現場で孤軍奮闘されている方へ、また、日本で中国のオペレーションを管理している方へ少しでもお役に立てればと思い、発行させていただいております。我々は、生産現場、物流現場向けの業務カイゼンのためのシステムを製造販売しておりますが、システム導入に限らず皆様のご苦労、問題を解決する事を第一の仕事としております。
コストカイゼンを含めた様々なカイゼン事例がたくさん蓄積されています。その事例を皆さんでシェアすることが、最短距離での解決方法ではないかと思い、ニュースレターを発行しています。お問合わせや、お聞きになりたいことがありましたら、このメールに直接返信して頂いて結構です。
当研究会では、しつこい売り込みは一切ないので、安心してお問い合わせ下さ
い。
**********************************************************
当研究会の理念は「感謝」です。
当研究会の仕事は、「現場で起こった問題をトヨタ生産方式(TPS)
やITを活用して解決し感謝される事」です。現場で困ったら、まずはご一報を!!
相談無料です。
https://a.k3r.jp/a_sol/1861F1131C
*********************************************************
ご連絡は中国からは400-604-1765フリーダイヤル、24H365日受付中、
日本からは+86-21-6440-1765 /86-21-6432-5544
受付時間は平日9:00〜18:00までです。
担当:門脇 日本語、中国語両方OKです!!
生産、物流現場カイゼンNews Letterはこちら!!
https://a.k3r.jp/a_sol/1861F1131C0
https://a.k3r.jp/a_sol/1861F0912B69
現場カイゼン塾沪江网校のURLはこちら!!
https://a.k3r.jp/a_sol/1861F1131B59
**********************************************************
この定期カイゼン通信の配信停止をご希望の方は下記より手続きを受け付けております。メール配信解除は
こちら