おはようございます!
カイゼン研究会の池田です。
↓↓↓
プロフィールはこちら
いやーーーーーーーーーーー暑い
暑すぎます。
毎年のことですが、上海の夏は本当に暑いです。
そして上海梅雨入りとか言ってましたが、
疑いたくなるほど雨が少ない気がします。
先週金曜でしたでしょうか、夕方事務所に夕立がきました。
短時間で相当降ったので、帰りはいくぶん涼しく感じましたが、
「こんなもんかー」です。
このまま梅雨明けがきたら、私の中では2022年に梅雨は来なかった、
と記憶されることでしょう笑
と、まぁしょうもない前座はこれくらいにいしまして…
本日も設備をテーマに取り上げます。
池田といえば、この手の話、とりわけ【設備稼働見える化】の
話が多かったりするのですが、今回は見える化の話、するのやめます笑
そろそろ「またかよ…」と突っ込まれそうなので、今回は設備の話ですが、
見える化以外の切り口で書いていこうと思います。
ではいよいよ本題に入っていくのですが…
私が工場に訪問させて頂く際、特に設備稼働見える化の
システム案件でお邪魔させて頂く時に質問することがあります。
それが「可動率って…計算されていますか?」です。
「一応現場にデータをとらせて計算していますよ」
から
「恥ずかしながら全くそこはみていません」
まで、色々な回答を頂けます。
“可動率”という言葉は工場でいえば一般的ですが、
どんなデータを使ってどうやって算出しているのか、
算出方法は実は工場によって異なっていたりします。
ただ、多くの工場では生産実績と出来高と生産にかかった
時間から算出しているところがほとんどように見受けられます。
生産実績や生産にかかった時間は多くの場合、現場の人が
紙ベースで記入していることが多いため、言ってしまえば
性善説ありきの自己申告制です。
これが悪いか?と言われると、日本ではこれで回っているところが
まだかなりあるので、今回そこを突っ込むつもりはありません笑
とは言うものの、可動率については全くやっていないところから、
算出されたデータを定期的に会議にかけてカイゼンするような
動きをされているところまで、様々な工場がいました。
では次の質問です。
「サイクルタイムってどうされてますか?」
そして、この後期待している答えというのはこうです。
「弊社では定期的にサイクルタイムを計算して、
設備稼働開始直後のサイクルタイムを維持できているか、
経年劣化によるサイクルタイムの遅延が発生していないか
を管理しています。
もし、社内で管理している、設定されたサイクルタイムよりも
実績が遅くなっている場合、それを早くするためのカイゼン活動を行います。」
これがベストアンサーです。
しかし、可動率の質問の時とはうってかわって、
こんな回答をする工場はほとんどいなかったりします。
何故私がこんな質問をするのか?
それは、
『設備の運用においてサイクルタイムの
管理が超重要だから』
です。
例えば多くの方は、“可動率”というワードが出てくると、
一般的な反応としては“向上”という言葉が紐づけされたように飛び出してきます。
日本側からも「可動率を上げろ」というプレッシャー
受けている工場は少なくないと思います。
すると、中国側も可動率は100%に近づけようと知恵を絞って考えます。
極端な話、100%にしたかったら止まっている時間をゼロに
して生産し続ければ良いことになります。
ただここで一歩立ち止まってみて、【可動率】という言葉に目が
向き過ぎてしまっているのではないかと思い、
今回【サイクルタイム】を切り口のテーマに取り上げたわけです。
そして、これが今回のテーマである
【サイクルタイム(出来高)にこだわる】
ということです。
もっと言えば、【時間当たりの出来高にこだわって短縮する】ということです。
先に答えを簡潔にまとめてしまうと、以下3つが重要なメリットです。
残業代の削減に繋がる
無駄な設備投資の抑制に繋がる
工場スペースの節約に繋がる
一つ一つ説明していきます。
そもそも、工場には製品ごとに必ず予め設定されている
サイクルタイムがあるはずです。
本来であれば、これを基準にして何時間で何個生産できる、
という算段を踏んで、生産計画も組むはずです。
よって、この基準が狂っていないかどうかをチェックすることは、
ちゃんと利益が出せているのかに影響するほど重要なことです。
しかし厄介なことにこのサイクルタイム、設備で生産を行う
という性質上、理論的にはどうしても徐々に遅くなってしまいます。
これが経年劣化です。
例えば、とある設備が経年劣化で不良が出やすくなってしまった場合、
恐らく現場の中国人は不良を出さないように設備を修理、
調整することを一番に考えます。
すると、優先度としてスピード、つまりサイクルタイムは
二の次になるはずです。
明らかに遅いと違和感を覚えるかもしれません。
ですが、管理者の見えない現場レベルで、
「とりあえずスピード若干落としたら不良でなくなったから、
しばらくこれで使ってみて、不良が出なければあとでスピードを元に戻すよ」
なんていう対応をされた場合、恐らくそのスピードは
若干落ちたまま使われ続けます。
いきなりがくんと落ちたら誰でも気が付けますが、徐々に、
若干ずつ、というスピード低下が年々積み重なれば、
もう違和感を覚える人間はいません。
こんな具合にちょっとずつの生産スピードの遅れが生じている
可能性があり得るわけです。
こうなってしまうと、現場の実力と理論計算が確実にずれてきます。
そうなると、理論的には残業なしでもこの受注に対応できる
はずなのに、何故か残業が必要になる、なんていう現象も
起こってしまいます。
ここで1つ目の重要なメリットである、残業代の削減に繋がります。
サイクルタイムが短くなるだけで1日の生産量が増えるため、
残業を減らすことができます。
また2つ目のメリットとして、生産量が増えるということは、
無駄に設備投資をせずに済むかもしれない、ということです。
専用機などを除いて、ある売れ筋の製品の受注増に対応するためには
単純に設備を増やすことを考えますが、サイクルタイムを短縮する
ことで受注増にも対応できる可能性があります。
また、その受注増が一過性だった場合、購入してせっかく増やした
能力も受注が減れば不要になります。
つまり、必要最低限の設備で最大限の効果をあげるためには、
サイクルタイムを極限まで上げる必要があるわけです。
さらに、設備投資をする必要がなくなるということは、
それだけスペースも無駄に使わなくて良くなります。
これが3つ目のメリットに繋がります。
これが今回の切り口である、サイクルタイム(出来高)に
こだわって短縮する、という趣旨の意味です。
確かに設備の止まっている時間を出来るだけ短くして
可動率を上げる、ということは重要です。
しかし、そもそも今の実力のサイクルタイムは設定されている
サイクルタイムと同じなのか?
ここにメスをいれていければ、上記のようなメリットが生まれます。
これは、自分達では受注量を決められない中小企業だからこそ、
インパクトの大きい効果になると思っています。
ベストは稼働データの出力をシステム化することで、
この手のデータはすぐに見られるようになりますが、
まずは手動計算される、ということでしたら、品番ごとに
生産開始/終了時間と、生産データを現場からもらってきて
記録するようにしてみてください。
そこで平均値を出して今のサイクルタイムを算出して、
実力値と設定されているサイクルタイムを比較してみてください。
そこから始めるだけでも生産効率はぐっと向上するはずです。
本日は設備が止まっている時間を極力減らす、という視点も
もちろん大切なのですが、それだけではなく、別の切り口で
設備を良くする方法、ということでサイクルタイムの
話をさせて頂きました。
本日も最後まで読んで頂きありがとうございました!
P.S.
現在手書きで設備から稼働データ(動いている/止まっている/
生産個数など)を記録しているが、これをシステム化して
信憑性の高い確実なデータでカイゼンを行いたい
でも、この手の設備見える化は設備の改造などが必要で
費用が高くついてしまって、どうしても二の足を踏んでしまう・・・
という方に朗報です!
今までの設備からデータをとってくる方式では、設備の改造が
必要になるケースが多く、どうしても改造費用でシステム化の
金額が大きくなってしまう、ということがありました。
しかしこの度、カイゼン研究会が新たに開発したデータ取得
キットを使うことで、設備の改造が一切不要になります。
これにより、より手軽に設備の稼働見える化を実現することができます。
動いている/止まっている/生産個数などが取得可能です。
今まで設備の改造が必要なために、システム化を諦めていた方
この機会に是非一度ご相談ください。
詳細を聞きたい、というだけでも大丈夫です。
ご連絡方法は本メルマガに直接ご返信頂くか、
もしくは私の電話番号までご連絡ください!
池田携帯番号:18601746691
それではご連絡お待ちしております。
wechat(微信)でも配信中!!(中国語版も)
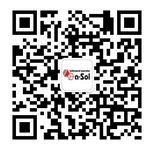
一般社団法人 生産、物流現場カイゼン研究会 中国支店
現場カイゼン診断士 池田 竜貴
==== この定期カイゼン通信の目的 ========
この定期カイゼン通信は、生産現場、物流現場で孤軍奮闘されている方へ、また、日本で中国のオペレーションを管理している方へ少しでもお役に立てればと思い、発行させていただいております。我々は、生産現場、物流現場向けの業務カイゼンのためのシステムを製造販売しておりますが、システム導入に限らず皆様のご苦労、問題を解決する事を第一の仕事としております。
コストカイゼンを含めた様々なカイゼン事例がたくさん蓄積されています。その事例を皆さんでシェアすることが、最短距離での解決方法ではないかと思い、ニュースレターを発行しています。お問合わせや、お聞きになりたいことがありましたら、このメールに直接返信して頂いて結構です。
当研究会では、しつこい売り込みは一切ないので、安心してお問い合わせ下さ
い。
**********************************************************
当研究会の理念は「感謝」です。
当研究会の仕事は、「現場で起こった問題をトヨタ生産方式(TPS)
やITを活用して解決し感謝される事」です。現場で困ったら、まずはご一報を!!
相談無料です。
https://a.k3r.jp/a_sol/1861F1131C
*********************************************************
ご連絡は中国からは400-604-1765フリーダイヤル、24H365日受付中、
日本からは+86-21-6440-1765 /86-21-6432-5544
受付時間は平日9:00〜18:00までです。
担当:門脇 日本語、中国語両方OKです!!
生産、物流現場カイゼンNews Letterはこちら!!
https://a.k3r.jp/a_sol/1861F1131C0
https://a.k3r.jp/a_sol/1861F0912B69
現場カイゼン塾沪江网校のURLはこちら!!
https://a.k3r.jp/a_sol/1861F1131B59
**********************************************************
この定期カイゼン通信の配信停止をご希望の方は下記より手続きを受け付けております。メール配信解除は
こちら