おはようございます。
一般社団法人 生産、物流現場カイゼン研究会 中国支店の鳥枝将光です。
(私のプロフィールは
こちら)
先週は今年最後となるカイゼン塾の1コース目に参加していました。
遠方の方は佛山、大連、烟台、武漢、東莞、山東からも参加いただいており、おかげさまで大賑わいでした。
業種で見ても、自動車部品、医療用部品、工具製造、金型製造、ソフトウェア(非製造業)、物流業など今回のクラスは特にバラエティに富んだクラスでした。
おかげさまで、今となってはカイゼン塾の運営や講義の大部分も私の"分身"である後輩に任せられるようになってきました。
とはいえ、11月のクラスは後輩がタイの展示会へ出張なので11月のコースでは私が表に出ることになりそうです。
(なんだかんだで私も現場が好きなのでたまにはいいなと楽しみにしています)
さて、今週の「Weekly 現場カイゼンブログ」をお届けいたします。
これは、「トヨタ 仕事の基本大全」という中経出版社が発行している本の中から、生産現場、物流の現場でお仕事されている方々にお役に立てる情報を、毎週1回当研究会の研究員から配信するものです。
「トヨタ 仕事の基本大全」という本の詳細はこちらです。
https://a.k3r.jp/a_sol/37137G8648B55
今週はCHAPTER_3 LECTURE31の"
「作業」と「ムダ」に分ける"です。
さて、ここで問題です。
まずは下記の動画を見てください。
https://a.k3r.jp/a_sol/37137G8648C64
(Youkuのページにジャンプします)
この動画は私が昼食でよく利用しているワンタン(馄饨)屋さんの作業の様子です。
(上海では有名なチェーン店です。全国展開してるのかな?)
あなたはこの動画見て、いくつの作業カイゼンを思いつきますか?
ちょっと考えてみてください。
…
さて、あなたはいくつの作業カイゼンが思い浮かびましたか?
1分20秒程の短い動画なので、何回が繰り返して見てくださいね。
もし、1、2個しか浮かばないようだったら、まだまだ隠れてますよ。
ヒントとして、トヨタの仕事大全ではこんなことが書かれています。
-----------------------
トヨタにおけるムダとは「付加価値を高めない現象や結果」です。
製造業で言えば「付加価値を生まず、原価のみを高める生産の要素」となります。
(中略)
人の動きには「正味作業」「付随作業」「ムダ」の3つがあります
ムダを取り除くことは当然で、付随作業をムダとみなして改善することもあれば、正味作業の中にも気づいていないムダが潜んでいることがあります。
トヨタではこうしたムダを徹底的に洗い出し、撲滅していくことが求められているのです。
-----------------------
さて、上記を踏まえた上で、答え合わせをするために道具などの呼称を一旦、以下の様に定義します。(私にも正式名称がわからないので…)
・ワンタンをいれてゆでている道具→カゴ
・半製品のワンタンが入っているプラスチックの容器→容器
・ワンタンのゆで汁をいれる道具→ひしゃく
・ワンタンをゆでている設備→ゆで器 とします。
それでは答え合わせをしてみましょう。
【作業カイゼン項目】
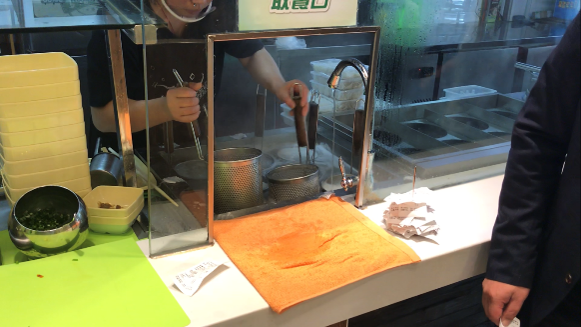
①仕上がり確認作業
→ゆであがり判断のためにゆで器からカゴを上げて確認する作業。
何度も繰り返されているがゆで時間などの客観的な判断基準ではなく、自己判断基準になっている可能性が高い。
[①カイゼン案例]
1.ゆで時間という基準での作業実施とタイマーの設置。
→ただし、現場では実作業中の水温はかなり波があるはずなので、繁忙期(昼食時間)
と閑散期(それ以外の時間帯)でゆで時間設定を変える必要がある可能性アリ。
→確認作業が消える代わりにタイマーのボタン押し作業が発生するので、作業時間で見て確認作業が無くなることで消去できる時間とタイマーのボタン押し作業が本当にトレードオフできるかの検証が必要。
2.ゆで時間以外での判断基準が作れないか?
→ワンタンが3個浮いてきたらゆであがりと判断できる、などゆで時間以外での判断ができないか?も検討に入れておく。
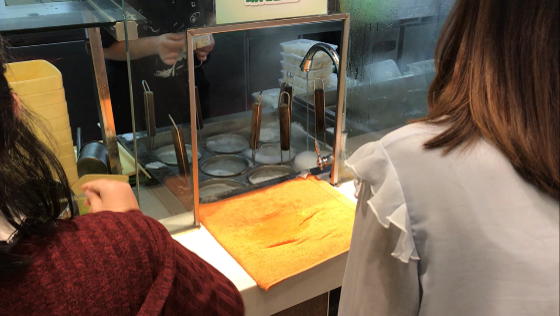
②包装のはぎ取り作業
→ラップが容器全体をラップで包んでいるため、両手が占有される。
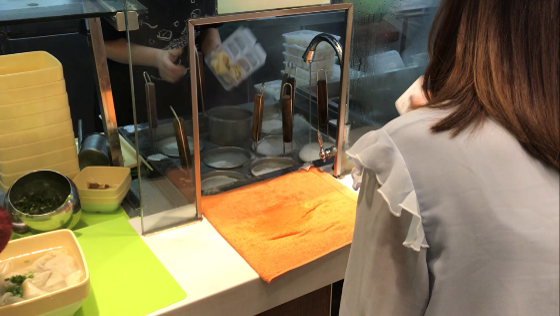
③容器→カゴへのワンタン投入作業が2回必要
→カゴは円形であるのに対して、容器は長方形となっているため、1個の容器に対してカゴへの投入作業は2回発生。
[②、③カイゼン案例]
②、③については、ゆで器が他の店舗でも円形かつ、サイズはほぼ変わらないことを前提として梱包・包装方法のカイゼン検討。容器のサイズ・形もゆで器のカゴに合わせる。
品質(味)には影響がないことをテストしながら、円形の容器、片手でも包装を剥がすことができないか?がテーマにカイゼン。片手包装剥がしについては冶具作成も視野に入れる。
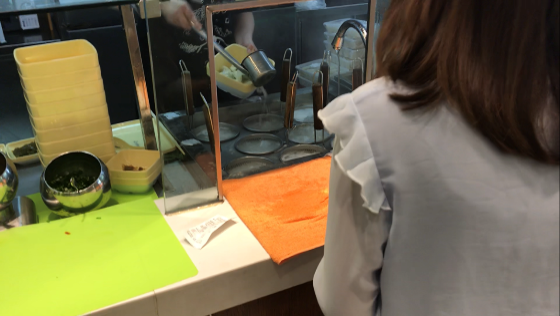
④カゴからお椀へのワンタン移動とゆで汁投入を一括作業にできないか?
→カゴからすべてゆで汁が抜けるため、ひしゃくでゆで汁をもう一度投入する必要がありお椀へよそう作業が2回必要。
[④カイゼン案例]
カゴを改造し、円筒の下半分は水が抜けない構造に改造できないか?
そうすることで一発でワンタンとゆで汁を移動できる方法はないか?
品質(味)に影響がないかを検証の上でカイゼン検討。
⑤容器や包装を捨てるゴミ箱の位置変更
→画面からゴミ箱は見えないが、恐らく膝程の高さにゴミ箱がある可能性が高い。
上半身を窮屈そうに曲げる作業が散見され、腰などにも負担が大きいと考えられる。
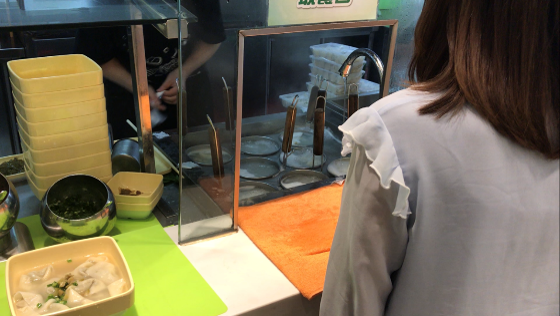
[⑤カイゼン案例]
ラクに作業できるよう高さや位置を変える。
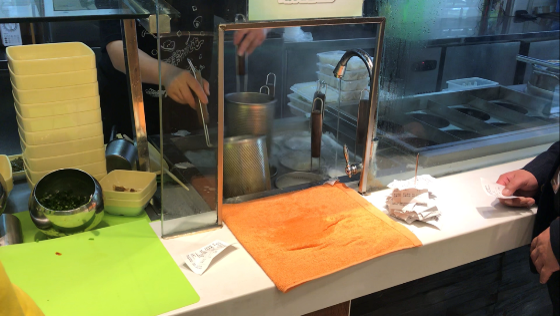
要注意(要確認)作業
・カゴと商品ラベルの位置替え作業
→一見、ムダですがこれには理由が潜んでいる可能性があります。
そもそもこの作業をする理由として考えられることは以下があります。
・手前からの水供給のためエリアによって温度が一定でない条件を解消するため
・ワンタン以外の商品(麺などの)ゆで条件の差異を埋めるための調整作業
作業者自身が経験を元にカンコツとして自然にやっている可能性があるのでこれはすぐにカイゼンではなく、現状調査が必要です。
また、ゆであがり確認のカゴ上げが水温の低下の要因の一つだと仮定される場合、①のムダが無くなることで、温度変化に違いが出る可能性があるためカイゼンしながらこのことも頭の片隅に置いておく必要があります
【作業以外の視点でのカイゼン検討項目】
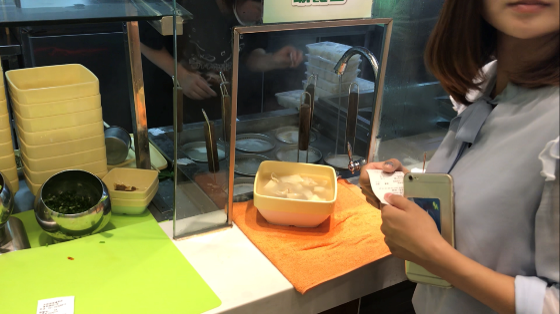
・ゆで器隣の丸い穴の空いた設備はいつ、どれくらいの頻度で使うのか?
→洗浄機?だろうか?
作る側からすると一等地を占められているため頻度に合わせてレイアウトを変えられないか?
または蓋を作って、不使用時は台として利用できるようにする など。
・ワンタン容器を縦に詰めながら並べているが、作業標準としてどの順番で重ねるか?が人によって違うと先入れ先出し(オーダー順序との不一致)が守れない可能性がある。
・この動画では撮れていませんが、実はお椀へ投入した後に完全にゆであがっていなかったためにもう一度カゴに戻す手直し作業が2回発生していました。
①の見直しが早急に必要です。
1分20秒ほどの動画ですが、5〜9個のカイゼン検討項目が考えられますね。
あなたはいくつ見つけられましたか?
(他にももっとたくさん見つけられましたか?)
私は個人的にもっとも身近な小ロット多品種生産は飲食店ではないか?
という考えを持っているので日常生活でもついつい作業の様子をじーっと眺めてしまいます。
おかげで、「あんた客じゃないのか?何見てんだ?!」と変な顔をされてしまうこともよくありますが…
とはいえ、視点を変えていろいろなものを見てみれば、森羅万象すべてのことが自分にとっての師となりうるものですね。
駐在生活も長くなり、新鮮味がなくなってきた頃こそ、改めて新しい視点で物事を見てみると新たな発見があるかもしれませんよ。
(大野耐一さんのカンバン方式の着想とアメリカのスーパーマーケットの話は有名ですよね)
あなたの現場がもっと良くなることを応援しています。
一般社団法人 生産、物流現場カイゼン研究会 中国支店
現場カイゼン診断士 鳥枝 将光
PS.
既にスタートした人気のカイゼン塾ですが、
コース別の分割参加ができるようになっています。
11月、12月のコースのみの参加もできますので下記をご覧ください。
https://a.k3r.jp/a_sol/37137G8648C53
実務者編、設備保全・管理者編ごとの詳細は以下をご覧下さい。
自ら問題を発見し、カイゼンを推進できる現場リーダー育成する、
現場カイゼン塾【実務者編】の詳細は以下です。
↓↓↓
詳細はコチラ
TPMを学び設備を故障したら修理する、から故障を予防し保全する
担当者育成を行う現場カイゼン塾【設備保全・管理者編】の詳細は以下です。
↓↓↓
詳細はコチラ
==== この定期カイゼン通信の目的 ========
この定期カイゼン通信は、生産現場、物流現場で孤軍奮闘されている方へ、また、日本で中国のオペレーションを管理している方へ少しでもお役に立てればと思い、発行させていただいております。我々は、生産現場、物流現場向けの業務カイゼンのためのシステムを製造販売しておりますが、システム導入に限らず皆様のご苦労、問題を解決する事を第一の仕事としております。
コストカイゼンを含めた様々なカイゼン事例がたくさん蓄積されています。その事例を皆さんでシェアすることが、最短距離での解決方法ではないかと思い、ニュースレターを発行しています。お問合わせや、お聞きになりたいことがありましたら、このメールに直接返信して頂いて結構です。
当研究会では、しつこい売り込みは一切ないので、安心してお問い合わせ下さ
い。
**********************************************************
当研究会の理念は「感謝」です。
当研究会の仕事は、「現場で起こった問題をトヨタ生産方式(TPS)
やITを活用して解決し感謝される事」です。現場で困ったら、まずはご一報を!!
相談無料です。
https://a.k3r.jp/a_sol/1861F1131C
*********************************************************
ご連絡は中国からは400-604-1765フリーダイヤル、24H365日受付中、
日本からは+86-21-6440-1765 /86-21-6432-5544
受付時間は平日9:00〜18:00までです。
担当:門脇 日本語、中国語両方OKです!!
生産、物流現場カイゼンNews Letterはこちら!!
https://a.k3r.jp/a_sol/1861F1131C0
https://a.k3r.jp/a_sol/1861F0912B69
現場カイゼン塾沪江网校のURLはこちら!!
https://a.k3r.jp/a_sol/1861F1131B59
**********************************************************
この定期カイゼン通信の配信停止をご希望の方は下記より手続きを受け付けております。メール配信解除は
こちら